After the HAI P44 press line at the Soest plant was fitted with a new extrutec profile cooling system over Christmas 2022/2023, the conversion of the power supply to the induction taper furnace from 1993 was realised in summer 2023.
The original Elhaus gas furnace and the furnace control system for preheating were replaced by extrutec back in 2012.
The switchgear of the induction taper furnace was originally designed as a masonry circuit with a balancing device.
Due to the mechanically operating load contactors, which switch on the load zones and the balancing circuit, which cause an asymmetrical mains load depending on the load case, the original design now had a number of significant disadvantages. Due to the age of the mechanically stressed switchgear, the focus was also on aspects such as optimised process control and significantly improved energy efficiency.
The extrutec scope of delivery for this conversion project included the following work:
- Conversion to state-of-the-art IGBT converter technology with extrutec Power Focus technology and integrated energy management system as a so-called uncompensated converter of the MIBu type, which can operate without compensation capacitors
- A complete new control system based on Siemens TIA Portal which is linked to the main control system
- Conversion of the block storage (tray conveyor) in front of the furnace (block preloading transfer table)
- 800 KVA power transformer and renewal of the power distribution system
- New water recooling system with frequency-controlled pump
- Modification of conveyor technology - components such as push-back rod and block conveyor system between gas and induction furnace
Due to the high capacity utilisation of this press line, the conversion was divided into three sections in consultation with our customer HAI, so that the conversion could also be carried out during the year at weekends, including public holidays.
The objectives of the furnace conversion were
- Uniform grid load in every operating state
- Mains power factor independent of load behaviour
- Stepless power control
- Constant power at each sub-zone as the inverter can operate in constant power mode.
- PID control behaviour
- Extrutec Power Focus TechnologyTM = better utilisation of the power unit
- Utilisation of the available space and the existing power distribution with minimal changes
- Utilisation of the original induction furnace, which has, however, been continuously improved over the years
- Improved energy efficiency, which was made possible in particular by the elimination of the balancing circuit and the compensation capacitors, as well as a new recooling system.
The conversion of this challenging project was completed on time in summer 2023 and impressively demonstrates that targeted measures can achieve significant improvements even in older existing systems at reasonable investment costs.
A project like this can only be realised flawlessly if many experienced experts work together. This expertise is available at extrutec in the induction technology/electric furnace construction division under the management of Stefan Beer. Complex conversion and modernisation projects can be implemented worldwide.
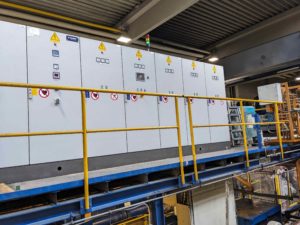