Eco Heating
Process (EHPTM)
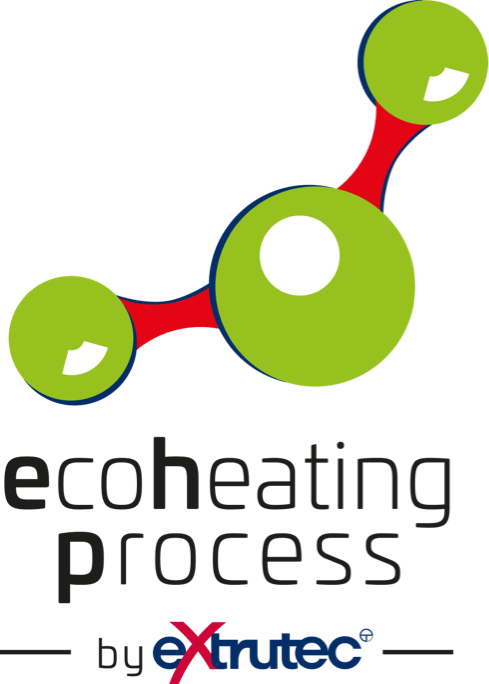
Energy efficiency
as a success factor
In addition, extrutec GmbH would like to make its contribution to the conservation of resources and against climate change. Therefore, the Eco Heating Process will be further optimized and supplemented with new technologies in the future.
Process flow
Process step 1: Preheating
- In the first process step, the aluminum bars coming from the bar magazine are fed to the new extrutec ESU (Eco Shower Unit). There, the bars are preheated from room temperature to temperatures of up to 90°C by laminar wetting of the entire bar surface with warm water.
- The Eco Shower Unit (ESU) uses the residual heat from the exhaust gases of the gas furnace downstream of the preheating zone and generates the required hot water in an air-water heat exchanger developed in-house. The ESU has a separate and closed water circuit consisting of a tank, circulation pump, self-cleaning filter and an integrated demineralization system.
- The water that is discharged due to evaporation losses (approx. 2 l/h) is automatically refilled, controlled via float switches. The entire system, including the roller conveyor acting as a base frame, is made of corrosion-resistant material (mainly stainless steel).
- In constellations with pure gas-fired convective heating, it is also possible to use the heat generated for the ESU, thus further increasing the efficiency to up to 90% and reducing the emissions accordingly.
Process step 2: High-convection preheating zone
- After preheating by the ESU, the aluminum bars then enter the high-convection preheating zone of the gas furnace. Here they are further exposed to flue gases from the direct gas-fired burner zones of the furnace and heated to up to 200°C.
- The aluminum bars are then passed through the ESU to the high convection preheating zone of the gas furnace. In the further process, the bars are then heated to approx. 400°C in the gas furnace.
The efficiency of a system as described above, consisting of ESU, gas-heated preheating furnace with preheating zone and downstream "in-line" inductive final heating, can be assumed to be approx. 75%.
„By 2025 at the latest, the German economy should be climate neutral".
In order to promote the minimization of greenhouse gases, the funding guideline "Decarbonization in Industry" of the Federal Ministry for the Environment came into force on January 1, 2021 for energy-intensive industrial sectors. A total of around 2 billion euros is available for this purpose up to 2024.
Machines and systems from extrutec, in particular the EHP(TM), are highly eligible for funding. The contact for the BMU funding program is the Competence Center for Climate Protection in Energy-Intensive Industries (KEI) in cooperation with the Federal Environment Agency (UBA). In a two-stage application process, the project is evaluated in terms of energy savings and approved. All relevant information is summarized here: klimaschutz-industrie.de
If you have any questions regarding technical details or consumption data of our plants, please do not hesitate to contact us.
Consulting
How may we help you?
We offer advice in all matters regarding heating, cooling, and material handling, and help you find technical solutions for your ideas. Our experience and know-how in the field of heating technology for forming processes, heat treatment concepts in aluminium extrusion plants, and a wide range of special solutions allow us to point out available options and to advise you on choosing the best concept for your specific requirements.
We also help you in planning, support you with new acquisitions, analyse the potential of your existing plants or processes or show you existing improvement possibilities.

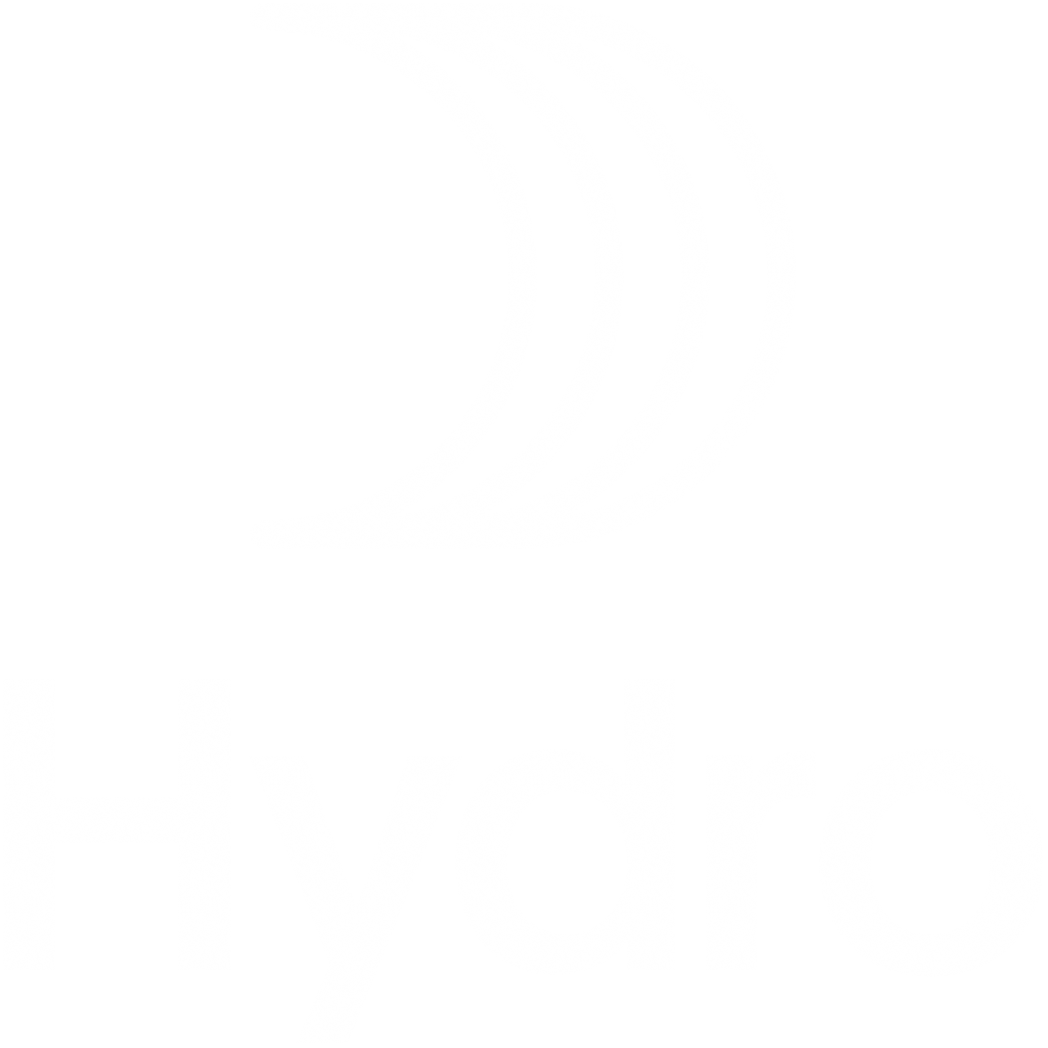
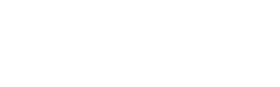
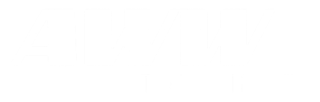
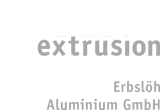

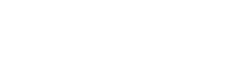
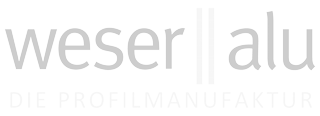
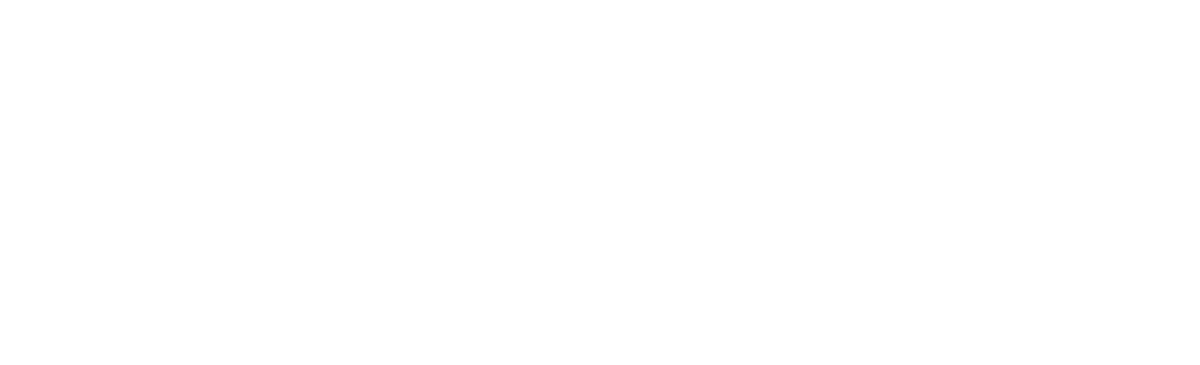