Future-oriented company development -
Michael Schindler and Jan Günter granted power of attorney
As part of extrutec GmbH’s ongoing strategic development, Michael Schindler and Jan Günter have been appointed as authorized signatories.
The past few years at extrutec have been defined by steady growth and innovation. Highlights include the establishment of our induction technology division and the launch of our own production facility. With the introduction of the EHKO – (electrically resistance-heated highspeed-convection oven)– we successfully addressed the increasing demand for efficient, hybrid, electricity-based heating systems.
To manage this dynamic growth, extrutec has simultaneously restructured and optimized its organizational framework. Dedicated departments have been established, and workflows from R&D to operations have been refined.
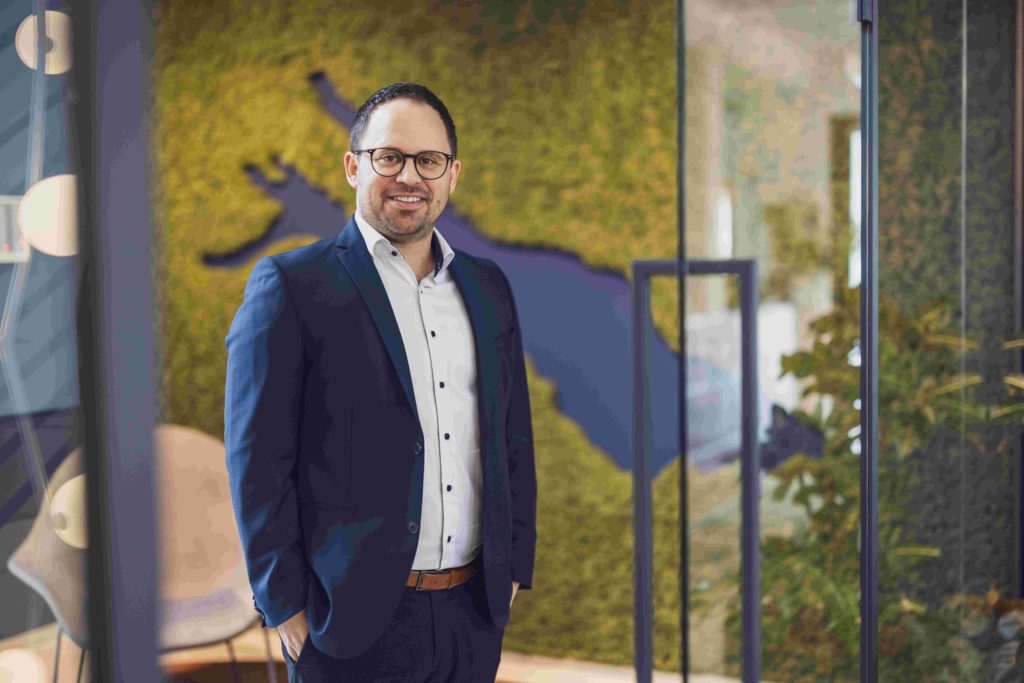
To support this momentum, the management team has been expanded with two new leaders. Michael Schindler now heads the Commercial Division. He joined extrutec in mid-2024 and moved from a similar position to the global technology leader in extrusion heating systems. His current focus is on HR and recruitment – a response to the rising demand for qualified professionals driven by our growing order volumes.
“I see great potential at extrutec not just in extrusion engineering but especially in innovation. And that requires motivated and dedicated people. Recruiting and supporting them is key to ensuring our long-term competitiveness,” says Michael Schindler.
Jan Günter takes on responsibility for Sales and Business Development as Business Unit Manager. His role includes oversight of our sales and aftersales teams, as well as the IT department – where he is driving forward digitalization initiatives.
“We’re noticing that many industry peers are cutting back on service. This creates frustration for customers – both new and existing. We’re taking a different path: investing heavily in our service department, especially to meet growing demand in regions like Asia,” explains Jan Günter.
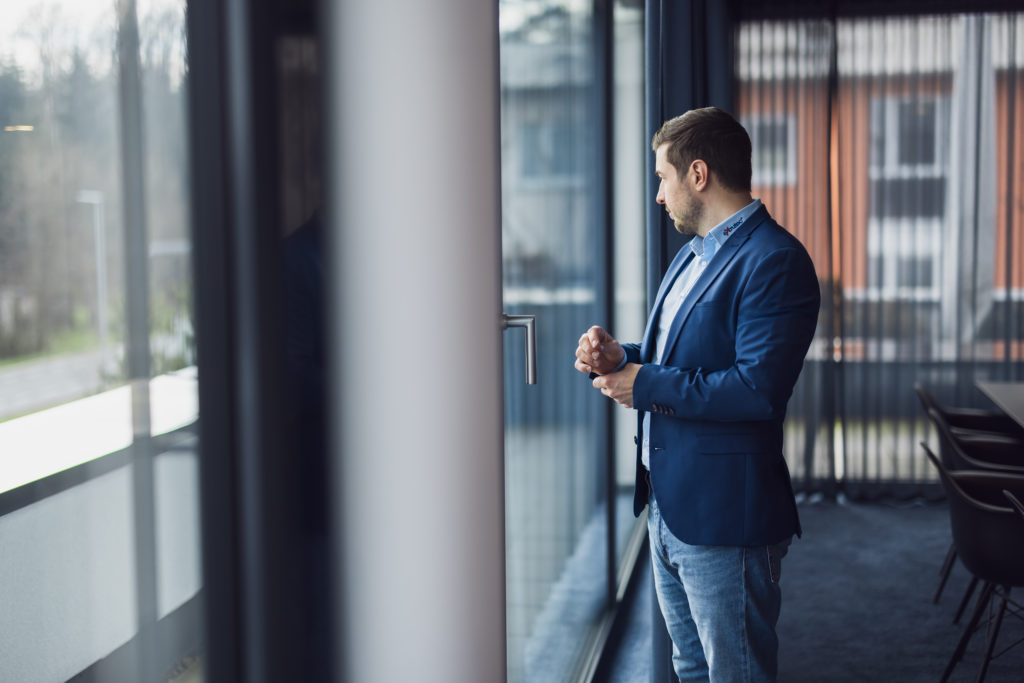
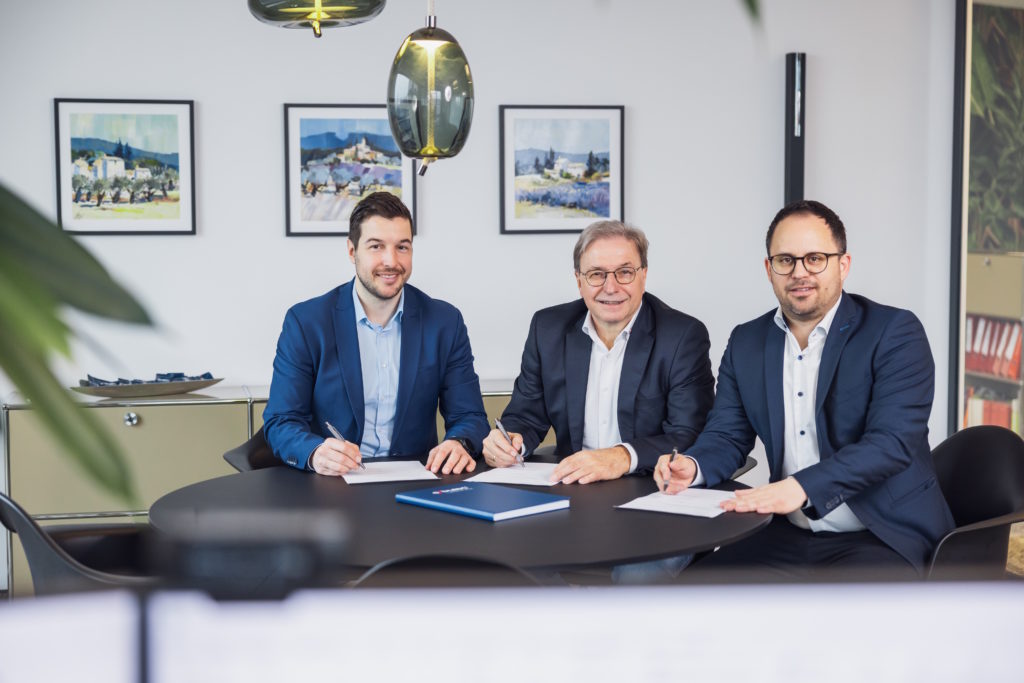
Managing Partner and owner Uwe Günter is delighted with both additions to the management team: “We must continue evolving across all areas – and that’s only possible with committed, qualified employees.”
The appointment of Michael Schindler and Jan Günter also reflect extrutec’s long-term succession strategy as authorized signatories. Uwe Günter will continue to accompany the business as managing partner until 2030, ensuring a smooth handover to the next generation of the family business.
News

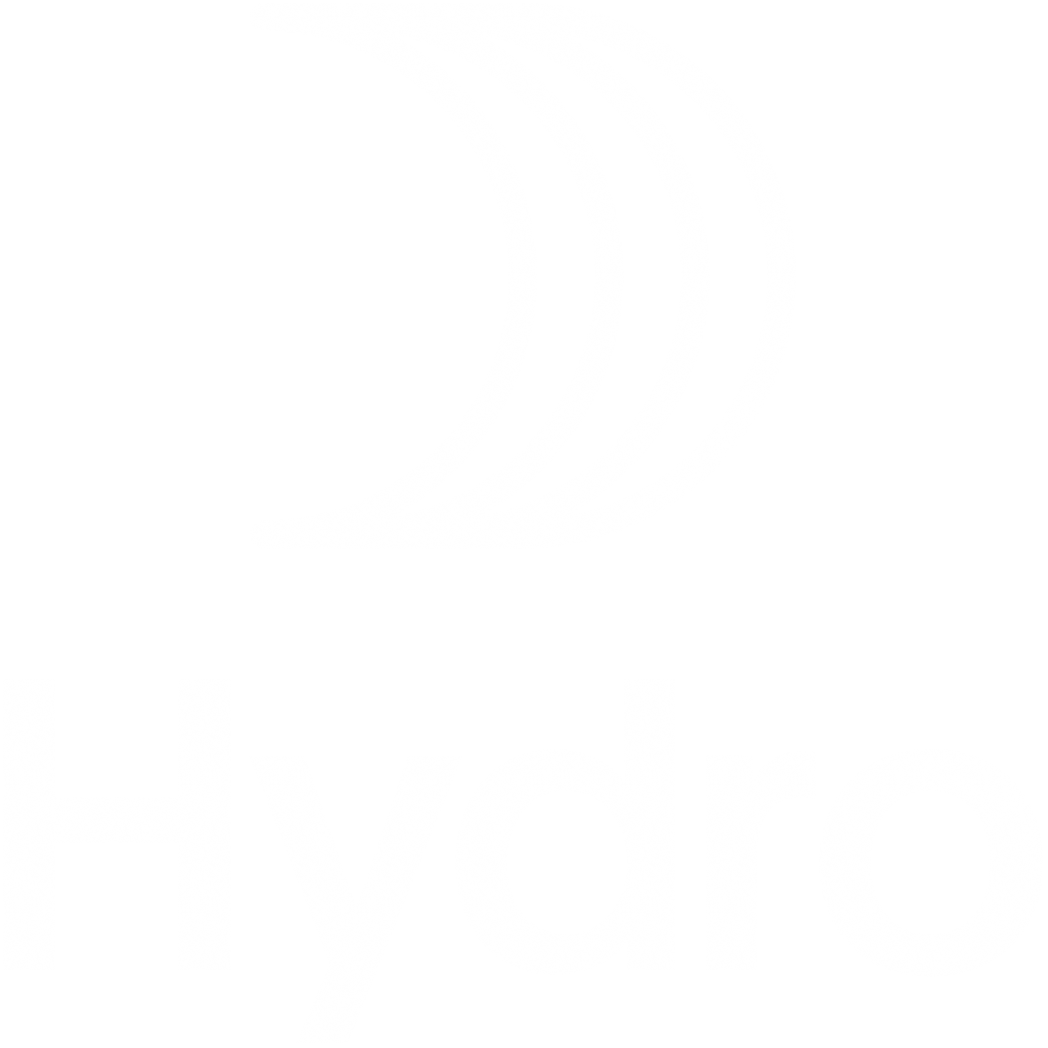
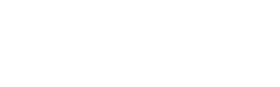
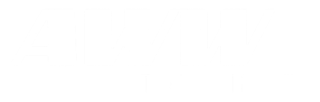
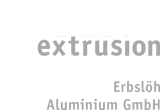

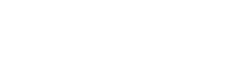
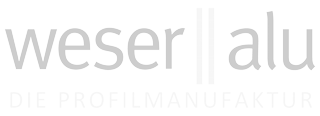
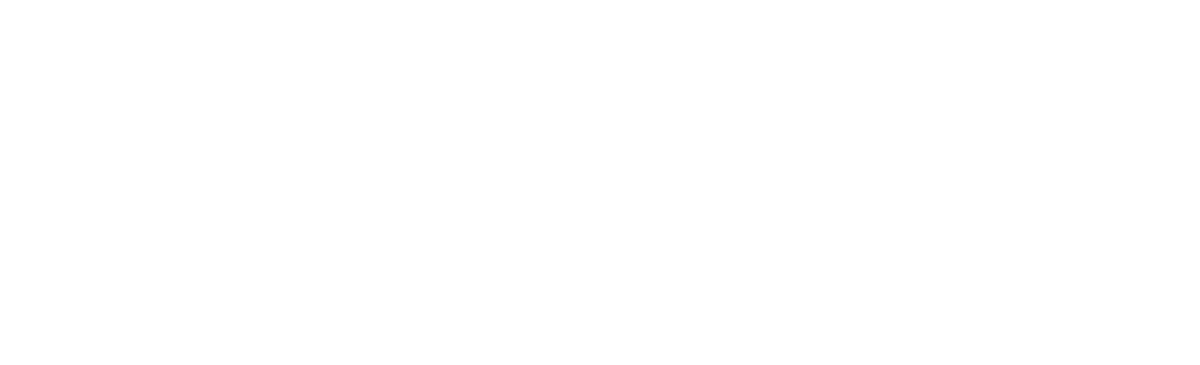